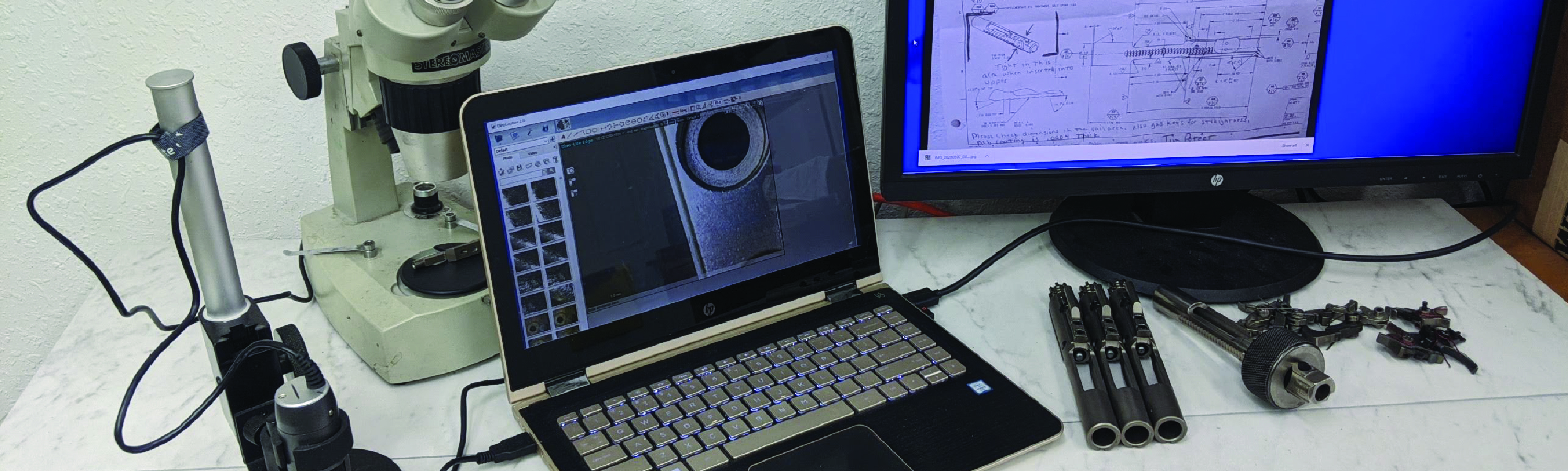
About Our NIB-X® Nickel Boron Technology
When formulated and applied correctly, a nickel boron finish will protect a substrate from corrosion, wear, solvents and heat. Learn more about this exceptional firearms coating and how our NiB-X® nickel boron formula helped make it the standard in the gun industry.
What Is Nickel Boron?
First developed in the 1960s, nickel boron (NiB) is a hard, naturally slick, corrosion-resistant alloy consisting of nickel and boron in different ratios. With the correct ratio and application method, nickel boron outperforms hard chrome, its industrial predecessor, while also being nontoxic, safer to work with and much more environmentally friendly.
Since the material’s inception, scientists have introduced various “grades” or “generations” of nickel boron designed to suit different applications. Most nickel boron formulas used today are either DMAB (containing 0.1% – 3% boron and used in the electronics industry for solderability improvement and circuit board bonding) or generation 3 (with 2.5% – 4.5% boron and up to 6% thallium). Generation 3 coatings yield a low coefficient of friction and chemical and corrosion resistance but lack the density and hardness of higher-boron formulas, making them less suitable for high-wear applications like coating firearm components.
What Is NiB-X®?
WMD Guns’ NiB-X® is a generation 5 nickel boron formulation with 4.5% – 6% boron content, which maximizes the hardness and wear resistance of the coating and optimizes the performance properties. This ratio is critical because high-wear parts demand formulas containing more boron to be able to withstand repeated exposure to heat and friction. Application thicknesses can range from a minimum of .0003” up to .005” in extreme-wear applications. Its natural bright, silvery color also looks extremely appealing on visible components.
When applied as a plating for a purpose-built component, generation 5 nickel boron gives the substrate a virtually impenetrable finish that resists wear, heat and chemical damage* without adding excessive thickness. That’s why it’s critical to work with an expert nickel boron applier who can tailor their coating to each specific workpiece.
How Is NiB-X® Nickel Boron Applied?
We apply NiB-X® using an electroless plating process, which means there is no electric current required for adhesion of the alloy. The formula joins with the substrate via an autocatalytic reaction, becoming a truly bonded surface finish rather than a mere buildup on the outside.
Electroless nickel boron plating first requires a thorough surface preparation process to ensure the desired performance from the resulting deposit. The deposit conforms to the surface of the part exactly — a feature that can be taken advantage of and gives the user a degree of flexibility in final texture that other coatings, platings, thin films and heat treatments do not.
With the bare metal exposed, the component to be plated is submerged in the nickel boron bath. To ensure a successful NiB plating process, the applicator must confirm that the solution contains the optimized chemistry ratios.
The length of time the part spends in the nickel boron coating tank is determined by the desired coating thickness. While it is possible to achieve thicknesses of up to .005”, the target is usually much lower, simply because a thicker layer isn’t necessary — nickel boron yields its excellent protective properties with only a thin layer, so it can be applied to firearms components without major changes to their critical dimensions.
The NiB is then finished per our design or the customer’s specifications, which we determine during the application development collaboration with the customer at the start of the project.
What Are the Benefits of a NiB-X® Finish?
If you’ve ever seen or handled a firearm finished in properly formulated nickel boron plating, you’re aware of one of the most obvious advantages of an NiB coating — it looks fantastic. However, the performance benefits give you plenty of other reasons to look into a nickel boron finishing service:
Increased Hardness
NiB-X® nickel boron obtains a hardness range of 1200-1400 knoop, an equivalent of 70+ on the Rockwell C scale — a measurement standard used for heat-treated, hardened steels. As such, it is harder than any metal in the firearm, offers extreme resilience against wear and boasts incredible longevity in harsh environments.
Superior Adhesion
Electroplating requires a current, and electricity travels along the path of least resistance. As a result, this process yields an inconsistent layer of the deposited alloy. In contrast, electroless nickel boron plating involves a simple submersion in a heated bath, so the nickel boron thoroughly bonds with every exposed surface — even inside crevices and other hard-to-reach areas. This property makes it perfect for components with complex features and contours, such as bolt carrier groups (BCGs).
NiB-X® has a superior bond when compared with either nickel teflon or other duplex coatings. With 20-30% teflon in the coating matrix, there is 20-30% teflon at the bond line, which impedes bond in those areas. This weakens the bond line integrity and tends to promote chipping and flaking under sliding and abrasive wear conditions.
Low Coefficient of Friction
Another factor that contributes to nickel boron’s long life span is its natural lubricity. NiB-X® is an inherently slick plating for metallic components, allowing assemblies to function faster and more smoothly even when they’re dirty — this characteristic makes nickel boron plating the perfect finish for AR parts since they’re subject to carbon buildup due to the platform’s direct gas impingement design. NiB-X® coated gun parts are therefore easier to clean and much more reliable.
Heat Resistance
Nickel boron plating has a melting point of 1,976 degrees Fahrenheit, making it perfect for components that undergo regular exposure to heat. With its heat and wear resistance, this coating is excellent for parts like AR-15 barrel extensions and BCGs.
Corrosion Protection
Aside from politicians, rust represents one of the greatest threats to a firearm. A nickel boron finish counters this danger by protecting metallic substrates from corrosion. Since electroless nickel boron plating reaches every surface on a submerged component — even in blind holes and crevices — it provides an exceptional degree of protection.
Why Choose WMD’s NiB-X® Nickel Boron Over Other Nickel Boron products?
The success we have had in introducing high-quality, nickel boron coated products to the firearms market has initiated a number of efforts from latecomers to offer “nickel boron” products. Some products have proved outright fraudulent, with companies claiming to have their parts coated in nickel boron while actually using an inferior formula.
Others have tried coating shops that don’t specialize in firearms or nickel boron plating. Because these shops are new to applying nickel boron, the products suffer from poor adhesion and poor coating quality, so they don’t reap the full benefits of a professionally applied NiB finish. Meanwhile, others use inferior materials in their products to save money and then coat them to try to hide the defects — what we in the industry call polishing the proverbial turd. All of these alternatives lead to performance issues when put into service.
Lastly, there are shops using very low-boron-content formulas (0.1-3% boron), known as DMAB, for firearms applications. DMAB is used primarily in the electronics industry as a soldering aid and is NOT a wear coating, meaning it’s unsuitable for use on firearms and will eventually flake or wear through, leaving your gun’s bare metal exposed to the elements.
WMD Guns’ nickel boron coatings are different because we use the correct amount of boron and maintain tight control of the materials and application at every phase of the coating process. The -X in NiB-X® stands for more than eXtreme durability, performance and reliability — it includes eXpert chemistry, processing, application and engineering. All of these things go into making WMD Guns the leading name in the business:
- Precise chemistry: NiB-X® is a proprietary nickel boron formulation produced entirely in-house at WMD — you can not procure it from a chemistry supplier as a standard off-the-shelf product. Thus, we maintain exacting control of the properties of the coating we apply. NiB-X® contains no lead in the coating and optimizes the hardness-lubricity balance in its properties.
- Advanced facilities and processes: NiB-X® is applied in our two high-volume, high-quality production facilities. Nickel boron plating is a very difficult technology to control, so it’s challenging to deliver consistent quality — the ordinary mom-and-pop shop cannot just install a tank and start running the technology with success. Additionally, real nickel boron must be certified to ASTMB607 and/or AMS2433C. Every WMD order can be certified to these specifications.
- Skilled application: A staff of metallurgists, chemists and plating engineers collaborate daily with gunsmiths, engineers and industry professionals to ensure that each new part is engineered with the optimal coating parameters. Nickel boron is not a “dip and ship” technology. It requires proper application development to be performed in order to be successful. This combination of talent within one team is very unique in the industry.
- Collaborative engineering: At WMD, we engineer our products for the coating technology we intend to use. We have seen products sent to us by customers who bought parts from an entrepreneurial vendor who had excess stock and decided to just coat pieces with off-the-shelf nickel boron because it’s the “hot” coating. This vendor sent the cheapest materials to the cheapest coating shop they could find — and the results are exactly what you’d expect. There is a tremendous difference in the outcome when the product is manufactured with the coating in mind. Additionally, when working with OEMs, the WMD Guns staff ensures proper application engineering principles are applied to defining the specific part, material and tolerances to optimize the plating parameters.
What Are the Differences Between NiB-X® and Other Firearm Coatings?
The Rc70 hardness of NiB-X® makes it much harder than nickel teflon (~Rc45), and Melonite™ (Rc55). Additionally, the process temperature for Melonite™ and other salt bath nitrocarburizing is 1050°F, which is too high for many components.
Physical vapor deposition (PVD) coatings are harder than NiB-X®, but they can only be built up to 2-4 microns thick. What’s more, these coatings are line-of-sight only, so they can’t extend to inside diameters, often result in uneven application on complex shapes, and do not have the low coefficient of friction you get from nickel boron plating. As a result, NIB-X® provides higher reliability for longer and allows for reduced maintenance and easier cleanup.
Another coating often confused with nickel boron is electroless nickel with boron nitride particles, which is similar to nickel teflon. However, while NiB-X® is a single coating and maintains its structure throughout the thickness, nickel teflon and nickel boron nitride are duplex finishes with a layer of electroless nickel and then a thin layer of EN+ Teflon or EN+ Boron Nitride (.0001”-.0002”). With either, the teflon or boron nitride will eventually wear, leaving you with nickel alone and inferior protection. WMD does offer nickel teflon upon request, but since the process is of the same labor-intensity and cost of true nickel boron while yielding lesser performance, we rarely use it of our own accord.
Is Nickel Boron Better Than a Ceramic Coating?
In a word, yes. NiB-X® yields much better performance than a ceramic finish.The spray-on, bake-on finishing systems popular today are cosmetic only and offer very low hardness (measured in pencil hardness) and little wear resistance. Thus, when one of these finishes is applied directly onto steel, it will wear off when exposed to repeated friction, creating corrosion initiation sites on your components.
WMD does use these ceramics for color, but we apply them on top of NiB-X® and other more robust finishes, which yields a very different result — when the ceramic inevitably wears thin, our NiB-X® is still protecting the metal underneath.
What to Expect From WMD Nickel Boron Gun Parts
WMD Guns’ BCGs and other AR parts are engineered and built specifically for the coating, leaving them with precise dimensions and the capacity for unrivaled performance. Where other companies “dip and ship” using standard or substandard components, we know our target product before we begin.
With a WMD Guns nickel boron BCG for AR-platform firearms, you get permanently slick, easy-clean surfaces and component quality rated for tens of thousands of rounds. Our NiB-X® products carry a lifetime warranty because that’s how much we believe in them — and how rigorously they’ve been tested, both by our team and the U.S. government agencies.
Our nickel boron AR parts are guaranteed to resist chipping, flaking, spalling and thinning. If you take care of them, they’ll take care of you, for life.
*While nickel boron is resilient against chemical exposure, we recommend avoiding the application of solvents such as Hoppe’s No 9 Bore Cleaner, as they state they are “not to be used on nickel” and may compromise the finish. Since NiB-X® is naturally slick, buildup can be removed with a rag or soft brush and a light cleaning oil — no solvents required.